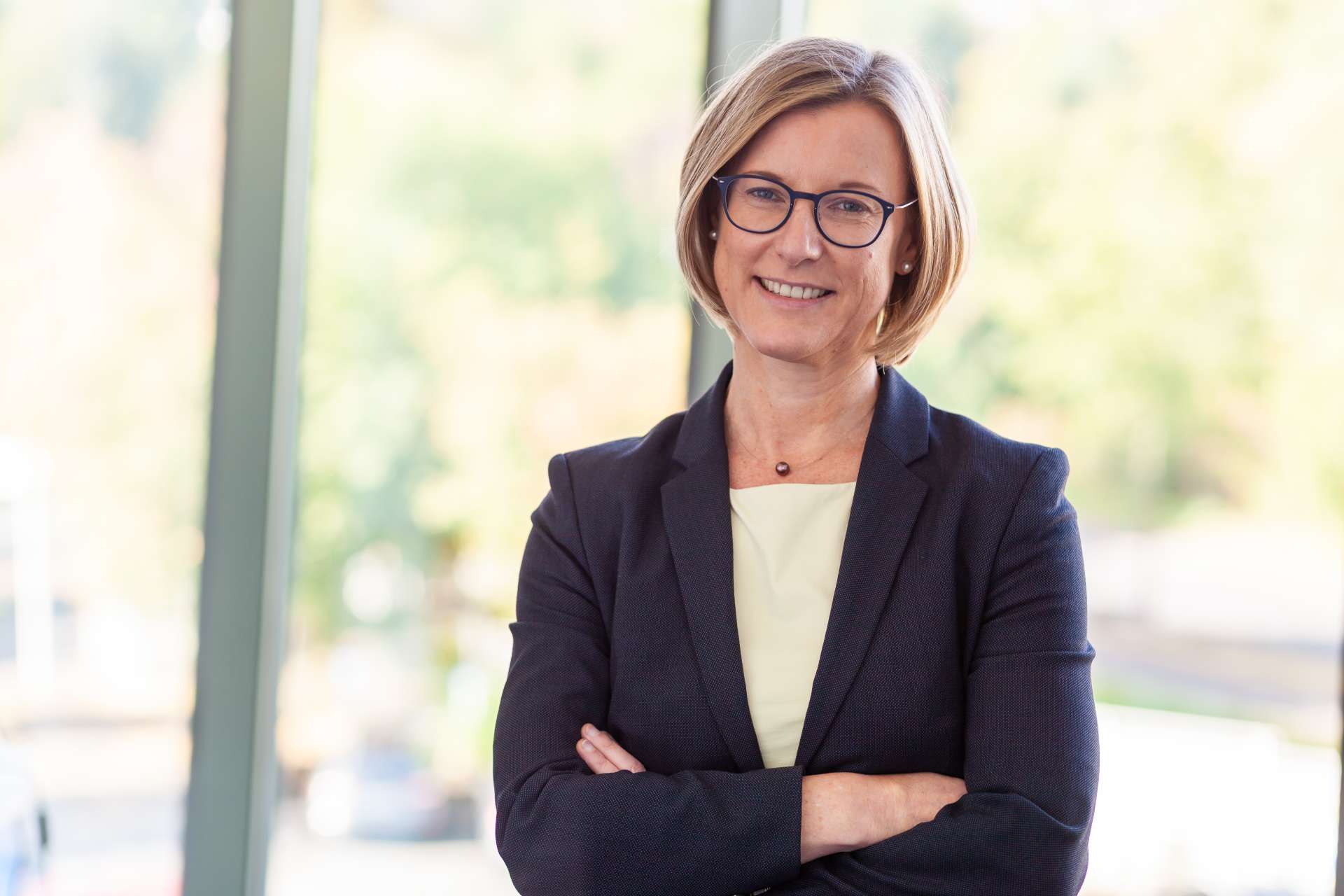
Interview mit Claudia Schaefer: Unser Streben nach kontinuierlicher Verbesserung von Effizienz, Qualität und Personaleinsatz
Als Corporate Senior Vice President of Production bei LTS hat Dr. Claudia Schaefer ein Auge auf Qualität und auf Effizienz. Hier erläutert sie die Faktoren, die eine kontinuierliche Verbesserung in beiden Bereichen zum Nutzen der Pharmakunden vorantreiben.
Auf das Wesentliche reduziert, kann man sich die Produktion als das Management des Gleichgewichts zwischen Angebot und Nachfrage vorstellen. In der heutigen schnelllebigen, digitalen Welt wird diese einfache Definition jedoch kaum der Komplexität und Koordinierung gerecht, die für dieses empfindliche Gleichgewicht erforderlich sind.
Im Jahr 2022 wurde der Druck auf das Angebot bei LTS durch einen erfreulichen Anstieg der Nachfrage nach zwei unserer gut etablierten Produktfamilien verstärkt: Hormonersatztherapie zur Unterstützung von Frauen in der Peri- und Postmenopause und Nikotinpflaster zur Unterstützung der Raucherentwöhnung.
Als Reaktion auf diese Situation konnten wir die Produktion im Vergleich zu 2021 um 27 % steigern und unseren bisherigen Rekord in Bezug auf die Anzahl der produzierten einzeln verpackten Systeme übertreffen. Das sind Spitzenergebnisse, auf die wir sehr stolz sind, und aus Sicht der Produktion gibt es viele Faktoren, die dazu beigetragen haben, dass wir sie erreichen konnten.
Zu diesen Faktoren gehört in erster Linie das Engagement unserer Mitarbeiterinnen und Mitarbeiter, sowohl in den operativen als auch in den unterstützenden Bereichen, deren Produktivität durch Sonderschichten und Überstunden ergänzt wurde, um die Produktion deutlich zu steigern. Dies wurde unter schwierigen Umständen erreicht, da die Pandemie in der ersten Jahreshälfte noch einen Schatten warf und die allgemeinen Herausforderungen auf dem Arbeitsmarkt zu einem ausgeprägten Fachkräftemangel führten, der bis heute spürbar ist.
Die Personalbeschaffung bleibt eine wichtige Säule unserer Wachstumsstrategie, um noch ehrgeizigere Ziele für 2023 zu erreichen. Parallel dazu sind wir bestrebt, unsere Prozesse zu optimieren, um sicherzustellen, dass wir unsere Ressourcen so effizient wie möglich nutzen. Außerdem investieren wir in zusätzliche Produktionsmaschinen und die dazugehörige Infrastruktur, um ein nachhaltiges Wachstum in der Hormonersatztherapie zu erreichen.
Diese Zukunftsvision wird durch den effektiven Einsatz von Technologie verbunden, und wir befinden uns derzeit in der Endphase des größten Digitalisierungsprojekts, das wir in Bezug auf unsere Produktionskapazitäten hier bei LTS durchgeführt haben. Die erste Phase dieses Projekts, die 2021 abgeschlossen wurde, basierte auf der Einführung eines Manufacturing Execution Systems (MES) – ein Softwaretool, das eine Schnittstelle zwischen unserer Produktionslinie und unserem SAP Enterprise Resource Planning System bildet.
Die Umsetzung dieser Phase erforderte eine umfassende Modernisierung unserer digitalen Infrastruktur. 92 Maschinen und Arbeitsplätze wurden an das SAP-System angeschlossen und durch die Installation von Tablets, Scannern und Touchscreen-Monitoren für die Nutzung durch rund 300 Kolleg:innen ausgerüstet. Das Ergebnis ist, dass wir nun den Maschinenstatus automatisch und in Echtzeit erfassen können, was das bisherige manuelle System der Aufzeichnung ersetzt. Die Daten zu den Ausfallzeiten fließen direkt in unser Werkstattmanagement ein, so dass wir täglich prioritäre Maßnahmen einleiten können. Längerfristig können wir Trenddaten zur Maschinenleistung analysieren, um kontinuierliche Verbesserungen umzusetzen und schlanke Produktionstechniken zu unterstützen.
Die zweite Phase des Projekts ist jetzt im Gange, und wir testen und validieren derzeit eine Software, die die interne Produktionslogistik verbessern und weitere Verbesserungen unter GMP-Gesichtspunkten bringen soll. Mit diesem System werden digitale 2D-Codes in unseren Materialbereitstellungsbereichen eingeführt, d. h. die Mitarbeiter an der Produktionslinie erhalten einen Auftrag und die zugehörige Stückliste auf einem Tablet zusammen mit dem genauen Standort der Materialien im Produktionsbereich. Die Artikel werden gescannt, damit das System sie digital auf ihre Richtigkeit überprüfen kann, während der Zeitaufwand für die Suche minimiert und potenzielle Fehlerquellen beseitigt werden.
Die Daten zu den verwendeten Materialien werden dann direkt in das SAP-System eingegeben, wodurch ein zuvor manueller Prozess digitalisiert wird, um die Datenintegrität zu gewährleisten und den Informationstransfer zu beschleunigen. Unser Abstimmungsprozess ist nun vollständig automatisiert, da wir unsere interne Materialhandhabung weiter optimieren und unsere GMP-Betriebsstandards weiter verbessern, um sicherzustellen, dass Fehlerquellen minimiert werden und die Datenintegrität optimiert wird.
Aus technischer Sicht handelt es sich um bedeutende Veränderungen, aber wir wissen, dass es auch wichtig ist, den damit verbundenen kulturellen Wandel anzuerkennen. Wir gehen diesen Aspekt mit unserem Team jetzt in der Umsetzungsphase an. So werden beispielsweise die entscheidenden Schritte der Softwareprüfung und -entwicklung unter Einbeziehung interdisziplinärer Teams durchgeführt, die sich aus Kolleginnen und Kollegen aus Planung, Qualität, Logistik sowie Lean-Fertigung zusammensetzen. Auch die Kolleg:innen aus der Produktion haben wir so weit wie möglich in diesen Prozess einbezogen, um ihr Feedback direkt in die Gestaltung der Software einfließen zu lassen. Denn sie werden später nicht nur selbst mit den Systemen arbeiten, sondern auch bei der Einführung als Fürsprecher fungieren und andere Teammitglieder mit ins Boot holen.
Für alle drei Produktionsschichten sind rund 40 Schulungen geplant, die sowohl Präsenzschulungen als auch Videolernmaterialien für die Schulung am SAP-System umfassen. Indem wir uns schrittweise an bestimmte Produktionsabteilungen wenden, können wir Probleme in jeder Phase der Einführung schnell erkennen und beheben und so alle Mitarbeiter:innen auf die effizienteste und effektivste Weise erreichen. Letztendlich ist es unser Ziel, eine bessere Produktion zu unterstützen, indem wir die Quelle möglicher Fehler möglichst gering halten, aber wir haben auch die Verantwortung, den Stress für das Team unter veränderten Bedingungen zu minimieren. Daher planen wir auch die Phase nach der Einführung, die darauf abzielt, die neuen Prozesse und Kenntnisse zu festigen und einen reibungslosen Übergang zur neuen Routine zu ermöglichen.
Mit Blick auf die Zukunft wird die Automatisierung eine immer wichtigere Rolle bei der Erzielung weiterer Prozessverbesserungen spielen, und unsere Konstruktionsabteilung bringt ihre Fähigkeiten in diesem Bereich zum Tragen. Ihre Fähigkeiten in der Maschinenkonstruktion und -entwicklung sind entscheidend für die Unterstützung kundenspezifischer Produktionsanforderungen, insbesondere für die Stanz- und Siegelschritte bei der Primärverpackung von transdermalen Therapiesystemen und oralen Wirkstoff-Filmen. Vor einigen Jahren haben wir ein erweitertes Spektrum an technischen Fähigkeiten in einem separaten Team – dem Team für Prozessoptimierung und Technologieintegration (POTI) – zusammengeführt, um Innovationen in den Bereichen Maschinenkonstruktion, Automatisierung und damit verbundene Fertigungsprozesse zu entwickeln. Seitdem hat das Team eine Maschine zur Automatisierung des Tertiärverpackungsprozesses entwickelt – ein traditionell arbeitsintensiver manueller Prozess, bei dem verpackte Artikel in einen Umkarton eingeschlossen werden, wie es von bestimmten Märkten gefordert wird.
Die Technologie basiert auf einer Roboter-Verpackungslinie, die am Ende der Sekundärverpackungslinie platziert wird. Die Maschine identifiziert die Tertiärverpackung, faltet sie auf, sammelt eine bestimmte Anzahl von Sekundärkartons ein, legt sie in den Tertiärkarton, verschließt ihn und übergibt ihn an den nächsten Prozessschritt, der eine Etikettierung mit Originalitätssicherung oder der Druck variabler Daten sein kann. Ein besonderes Merkmal der Maschine ist, dass sie sich auf der Grundlage des Materialcodes und der zugrundeliegenden Anweisungen selbst einstellen kann, so dass sie nicht nur einen Teil der manuellen Arbeit ersetzt, sondern auch die Einrichtung von Auftrag zu Auftrag hochgradig automatisiert ist, was zu weiteren Kapazitäts- und Zeiteinsparungen in unseren Verpackungslinien führt.
Dies ist nur ein Beispiel aus einer Vielzahl laufender Aktivitäten, die wir bei LTS im Hinblick auf die kontinuierliche Verbesserung unserer Produktionskapazitäten verfolgen. In den 20 Jahren, die ich hier arbeite, zunächst als Leiter des F&E-Labors und jetzt als Produktionsleiter, ist dies ein durchgängiges Thema. Mit Blick auf den Rest des Jahres 2023 und darüber hinaus sind wir zuversichtlich, dass dieser Ansatz – basierend auf einer nachhaltigen Investition in Technologie, Mitarbeiter:innen und Innovation – sicherstellen wird, dass wir die wesentlichen Faktoren von Nachfrage und Angebot auch weiterhin mit Zuversicht ausgleichen können.